Quando se trabalha com sistemas de tubulação, seguir as normas de flanges é essencial para garantir a segurança e a eficiência das instalações industriais. As flanges desempenham um papel fundamental na conexão de tubos, válvulas e outros equipamentos, permitindo a montagem e desmontagem com facilidade. Além disso, para realizar manutenções seguras e eficientes, muitas empresas recorrem à locação de separador de flange, um equipamento essencial para separar flanges com segurança.
Neste artigo, vamos explorar as principais normas de flanges, explicando de forma simples e direta o que você precisa saber para garantir que suas conexões estejam em conformidade com os padrões de segurança e qualidade.
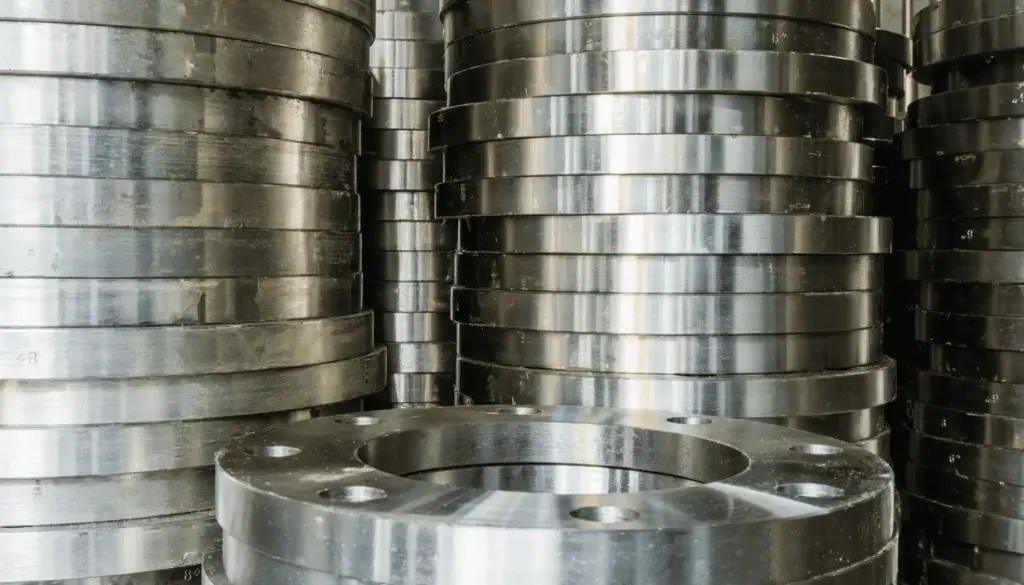
O Que São Flanges?
Flanges são componentes mecânicos utilizados para unir tubulações, válvulas, bombas e outros equipamentos industriais. Elas formam uma conexão segura que permite a desmontagem e manutenção de trechos de tubulação sem a necessidade de cortes ou soldas. As flanges são fixadas por meio de parafusos e utilizam juntas de vedação para evitar vazamentos e garantir a integridade do sistema sob pressão e temperatura.
Existem diferentes tipos de flanges, cada uma projetada para atender a condições operacionais específicas. Por exemplo, flanges com face levantada são usadas para garantir uma vedação mais eficiente em sistemas de alta pressão, enquanto flanges com face plana são indicadas para sistemas de baixa pressão. A escolha do tipo de flange depende de fatores como pressão de operação, temperatura e tipo de fluido transportado.
Outro aspecto importante das flanges é o material de fabricação. Elas podem ser feitas de aço carbono, aço inoxidável, ligas de níquel, titânio e até materiais plásticos, dependendo da aplicação. Flanges de aço inoxidável, por exemplo, são ideais para ambientes corrosivos, enquanto flanges de titânio oferecem alta resistência a temperaturas extremas e produtos químicos agressivos.
Além de unirem tubulações, as flanges também permitem a instalação de válvulas e outros componentes importantes no sistema. Isso facilita a inspeção e manutenção do sistema sem a necessidade de desmontar grandes trechos de tubulação. Em sistemas industriais complexos, essa facilidade é essencial para garantir a continuidade operacional e reduzir o tempo de inatividade durante paradas para manutenção.
Importância das Normas de Flanges
As normas de flanges são essenciais para garantir a segurança e a eficiência das conexões em sistemas de tubulação industrial. Elas definem critérios técnicos que padronizam o processo de fabricação, montagem e manutenção das flanges. Seguir essas normas evita problemas estruturais, como vazamentos, falhas em conexões e acidentes operacionais. Além disso, a padronização facilita a substituição e a manutenção das flanges, tornando o processo mais eficiente.
Outro fator importante é a segurança operacional. Quando uma flange está em conformidade com as normas, ela é capaz de suportar as condições de operação, como variações de pressão e temperatura, sem comprometer a integridade do sistema. Isso é fundamental em ambientes industriais de alta pressão, como refinarias, petroquímicas e plataformas de petróleo, onde qualquer falha pode resultar em acidentes graves.
Além da segurança, seguir as normas garante a interoperabilidade entre diferentes componentes. Isso significa que uma flange fabricada de acordo com a norma ASME, por exemplo, será compatível com equipamentos e tubulações que seguem o mesmo padrão. Essa compatibilidade facilita a montagem e desmontagem dos sistemas, reduzindo o tempo de parada para manutenção e melhorando a eficiência operacional.
Por fim, o uso de flanges que atendem às normas contribui para a longevidade dos sistemas industriais. Flanges certificadas são projetadas para resistir ao desgaste, corrosão e outras condições adversas, o que resulta em menos necessidade de substituição e menor custo de manutenção a longo prazo. Manter o sistema em conformidade com as normas também é um requisito em auditorias de segurança e qualidade, o que evita penalidades regulatórias e garante a continuidade operacional.
Principais Normas de Flanges
As normas de flanges são fundamentais para garantir a segurança e o desempenho dos sistemas de tubulação industrial. Elas definem critérios técnicos para a fabricação, montagem e operação de flanges, assegurando que as conexões suportem variações de pressão, temperatura e vibração sem falhas. O uso correto dessas normas evita vazamentos, falhas estruturais e acidentes, promovendo a eficiência e a segurança nas operações industriais.
Norma | Origem | Classificação de Pressão | Aplicação Comum |
---|---|---|---|
ASME (American Society of Mechanical Engineers) | Estados Unidos | Class 150 a Class 2500 | Petróleo e gás, indústria química e geração de energia |
ANSI (American National Standards Institute) | Estados Unidos | Class 150 a Class 2500 | Indústria química, processos industriais e construção |
DIN (Deutsches Institut für Normung) | Alemanha | PN 6 a PN 400 | Indústria europeia e química |
BS (British Standards) | Reino Unido | PN 6 a PN 400 | Sistemas de água e vapor |
Normas ASME para Flanges
As normas ASME (American Society of Mechanical Engineers) são as mais utilizadas em projetos industriais nos Estados Unidos e em muitos outros países. A ASME é responsável por estabelecer critérios técnicos para a fabricação, montagem e teste de flanges, garantindo que elas suportem condições extremas de pressão e temperatura sem falhas. As normas ASME são amplamente aplicadas em setores como petróleo e gás, indústria química, geração de energia e construção naval.
A norma ASME B16.5 define os requisitos para flanges de aço forjado, incluindo dimensões, materiais, classes de pressão e métodos de inspeção. Já a norma ASME B16.47 trata de flanges de grande diâmetro (acima de 24 polegadas), utilizadas em sistemas de alta capacidade. Essas normas especificam também os tipos de face (face levantada, face plana, anel de junta) e os tipos de acabamento para garantir a vedação eficiente.
Um ponto importante nas normas ASME é a classificação de pressão, que é definida em “Classes”. As principais classes de pressão na ASME são:
- Class 150
- Class 300
- Class 600
- Class 900
- Class 1500
- Class 2500
Essa classificação define a pressão máxima de operação da flange em função da temperatura. Por exemplo, uma flange Class 150 pode operar a uma pressão de até 19,6 bar (284 psi) a 38°C, enquanto uma flange Class 2500 pode operar a até 425,2 bar (6160 psi) na mesma temperatura.
Além disso, as normas ASME estabelecem diretrizes para inspeção e teste de flanges. Entre os testes exigidos, estão o teste hidrostático, o teste de impacto e o teste de resistência à pressão. Dessa forma, esses testes garantem que a flange será capaz de suportar as condições de operação sem apresentar deformações ou vazamentos.
Norma DIN para Flanges
As normas DIN (Deutsches Institut für Normung) são os padrões alemães para flanges, amplamente utilizados na Europa e em diversos setores industriais, como químico, petroquímico, alimentício e farmacêutico. As normas DIN estabelecem critérios detalhados para fabricação, instalação e teste de flanges, garantindo que elas sejam compatíveis com sistemas industriais complexos e suportem condições de alta pressão e temperatura.
Uma das principais diferenças entre as normas DIN e ASME é a forma de classificação da pressão. Enquanto as normas ASME utilizam o sistema de “Class” (Class 150, Class 300, etc.), as normas DIN utilizam o sistema de Pressão Nominal (PN). As classes de pressão nas normas DIN são definidas como:
- PN 6
- PN 10
- PN 16
- PN 25
- PN 40
- PN 100
- PN 160
- PN 250
- PN 400
Cada valor de PN (Pressão Nominal) representa a pressão máxima em bar que a flange pode suportar a uma temperatura de referência de 20°C. Por exemplo, uma flange PN 40 pode operar com uma pressão de até 40 bar a essa temperatura. Essa classificação facilita a seleção de flanges para diferentes sistemas de tubulação.
As normas DIN também definem o tipo de material utilizado na fabricação de flanges. Flanges DIN podem ser feitas de aço carbono, aço inoxidável, ligas de níquel, cobre e materiais plásticos reforçados. A escolha do material depende das condições operacionais, como tipo de fluido, temperatura e resistência à corrosão.
Além disso, outro ponto importante das normas DIN é a precisão dimensional e as tolerâncias exigidas. As flanges DIN seguem critérios rigorosos para o diâmetro dos furos, espessura da face, acabamento da superfície e posição dos parafusos. Essa atenção aos detalhes garante que a flange se alinhe perfeitamente ao sistema de tubulação, proporcionando assim uma vedação eficiente e segura.
Normas ANSI para Flanges
As normas ANSI (American National Standards Institute) regulam a fabricação e o uso de flanges nos Estados Unidos e em diversos outros países que seguem os padrões americanos. Elas estabelecem critérios para dimensões, materiais, métodos de vedação e classificação de pressão das flanges, garantindo compatibilidade e segurança nos sistemas de tubulação industrial. As normas ANSI são amplamente utilizadas em setores como indústria química, processos industriais, construção civil e transporte de fluidos.
Assim como nas normas ASME, as normas ANSI classificam as flanges em diferentes classes de pressão. As classes mais comuns são:
- Class 150
- Class 300
- Class 400
- Class 600
- Class 900
- Class 1500
- Class 2500
A classificação define a pressão máxima que a flange pode suportar a uma temperatura específica. Por exemplo, uma flange ANSI Class 150 pode operar a uma pressão de até 19,6 bar (284 psi) a 38°C, enquanto uma flange Class 2500 pode operar a até 425,2 bar (6160 psi) na mesma temperatura. Assim, essa padronização permite que os sistemas industriais operem com segurança em diferentes faixas de pressão e temperatura.
As normas ANSI também definem os tipos de face das flanges, que incluem:
- Face plana (Flat Face – FF) – Indicada para sistemas de baixa pressão e com menor necessidade de vedação.
- Face levantada (Raised Face – RF) – Usada em sistemas de alta pressão, proporciona uma vedação mais eficiente.
- Face com anel de junta (Ring Type Joint – RTJ) – Indicada para sistemas de alta pressão e alta temperatura, com uso de juntas metálicas para maior resistência.
Além disso, outro ponto importante nas normas ANSI é o controle de qualidade. Elas estabelecem métodos de inspeção e teste para garantir que as flanges atendam aos requisitos de resistência e vedação. Entre os testes mais comuns, estão o teste hidrostático, o teste de impacto e o teste de resistência à corrosão. Dessa forma, esses testes asseguram que as flanges possam suportar as condições operacionais sem falhas ou deformações.
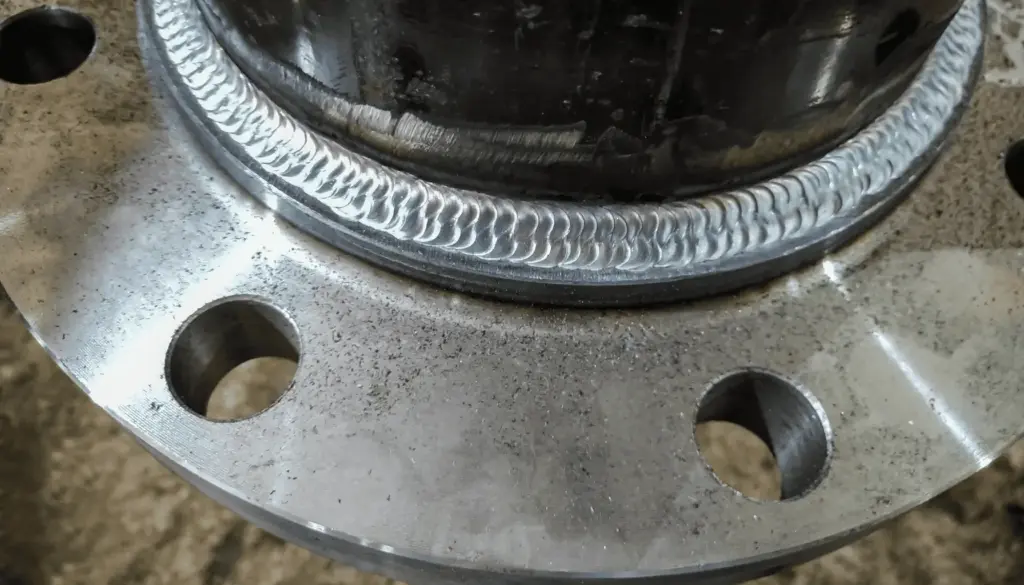
Classificação de Pressão nas Normas
A classificação de pressão determina a pressão máxima que uma flange pode suportar em uma determinada temperatura. Por outro lado, as normas ASME, ANSI e DIN definem diferentes sistemas de classificação, sendo assim essencial entender essas variações para evitar falhas em sistemas industriais. Portanto, a escolha da classe correta garante que a flange funcionará com segurança sob condições específicas de pressão e temperatura.
Nas normas ASME e ANSI, a classificação de pressão é expressa em “Classes” (150, 300, 600, 900, 1500 e 2500). Essas classes indicam a pressão máxima em psi que a flange pode suportar a uma temperatura específica. Por exemplo, uma flange Class 150 suporta até 285 psi a 38°C, enquanto uma flange Class 2500 pode suportar até 6160 psi na mesma temperatura.
Nas normas DIN, a classificação é definida em PN (Pressão Nominal), expressa em bar. As classes mais comuns são PN 6, PN 10, PN 16, PN 25, PN 40, PN 100, PN 160, PN 250 e PN 400. Uma flange PN 40, por exemplo, suporta até 40 bar a 20°C. Essa diferença entre ASME/ANSI e DIN requer atenção ao selecionar flanges para projetos internacionais.
O material da flange e o tipo de vedação também influenciam a capacidade de pressão. Flanges de aço carbono geralmente suportam pressões mais altas em temperaturas elevadas, enquanto flanges de aço inoxidável oferecem melhor resistência à corrosão. Consultar tabelas de pressão e temperatura fornecidas pelos fabricantes é essencial para garantir a seleção correta da classe de pressão.
Materiais Utilizados em Flanges
Os materiais utilizados na fabricação de flanges determinam sua resistência, durabilidade e desempenho em diferentes condições operacionais. As normas ASME, ANSI e DIN especificam quais materiais podem ser usados, considerando fatores como pressão, temperatura e exposição a agentes corrosivos. A escolha do material correto é essencial para garantir que a flange suporte as condições de operação sem falhas ou vazamentos.
Material | Resistência à Pressão | Resistência à Corrosão | Aplicação Comum |
---|---|---|---|
Aço carbono | Alta | Baixa | Sistemas de alta pressão e temperatura moderada |
Aço inoxidável | Média | Alta | Ambientes corrosivos e alta temperatura |
Ligas de níquel | Alta | Muito alta | Indústria química e petroquímica |
Titânio | Média | Muito alta | Ambientes agressivos e alta temperatura |
Plásticos reforçados | Baixa | Alta | Sistemas de baixa pressão e transporte de químicos |
Tipos de Juntas e Vedação
As juntas e os métodos de vedação utilizados em flanges desempenham, portanto, um papel fundamental para garantir que o sistema de tubulação permaneça hermético sob diferentes condições de operação. Além disso, as normas ASME, ANSI e DIN definem os tipos de juntas e os métodos de vedação recomendados para cada classe de pressão e tipo de flange. Consequentemente, a escolha da vedação correta evita vazamentos e falhas estruturais, aumentando assim a segurança operacional.
Sistemas de baixa e média pressão geralmente usam amplamente juntas de fibra, feitas de grafite, borracha e papelão hidráulico. Além disso, elas oferecem boa vedação em temperaturas moderadas. Por esse motivo, esse tipo de junta funciona bem em sistemas que transportam água, ar comprimido e fluidos não corrosivos.
Sistemas de alta pressão e temperatura usam juntas metálicas, feitas de aço inoxidável, cobre ou ligas especiais. Elas oferecem alta resistência mecânica e à corrosão. Flanges com face de anel (RTJ) geralmente usam essas juntas, que vedam por compressão mecânica.
Outro tipo comum é a junta espiralada, que combina camadas de metal e material de enchimento (como grafite ou PTFE). Esse tipo de junta é altamente flexível e se adapta bem a variações de pressão e temperatura. Juntas espiraladas são ideais para sistemas que operam sob condições extremas de temperatura e pressão, como em refinarias e usinas químicas.
Conclusão
Seguir as normas de flanges é essencial para garantir o funcionamento seguro e eficiente de sistemas industriais. As normas ASME, ANSI e DIN definem critérios técnicos para fabricação, montagem e operação de flanges, assegurando que elas suportem condições de pressão, temperatura e corrosão sem falhas. O uso correto de flanges certificadas reduz o risco de vazamentos e falhas estruturais, aumentando a segurança e a vida útil dos sistemas.
Além de garantir a segurança, respeitar as normas facilita a manutenção e substituição de componentes. Flanges fabricadas de acordo com normas internacionais são compatíveis com sistemas globais, permitindo maior flexibilidade na compra e instalação. Isso reduz o tempo de inatividade e os custos operacionais, garantindo maior eficiência nos processos industriais.
Se você deseja garantir que suas flanges estejam em conformidade com as normas ou precisa de orientação especializada para seleção, instalação e manutenção, entre em contato conosco. Nossa equipe técnica está preparada para fornecer suporte completo e ajudá-lo a escolher a melhor solução para seu projeto industrial.
A conformidade com as normas é um fator crítico para o sucesso de qualquer sistema de tubulação. Investir em flanges certificadas e seguir os critérios técnicos estabelecidos pelas normas é o caminho para garantir um sistema seguro, eficiente e durável em longo prazo.